در یک نگاه کلی و از نقطه نظر روشهای مرسوم تولید فولاد در ایران و در مقایسه با تکنولوژیهای تولید فولاد خام در جهان، به جرات میتوان قضاوت کرد. در گذشته و به دلیل ارزان بودن انرژی و دسترسی به ذخایر سرشار گاز طبیعی، تکنولوژی بسیار سخاوتمندانهای به عنوان روش اصلی تولید فولاد در ایران انتخاب شده و بنابراین عمده تولید فولاد خام ایران از آن زمان تاکنون بر همین اساس بنا نهاده شده است.
در یک نگاه کلی و از نقطه نظر روشهای مرسوم تولید فولاد در ایران و در مقایسه با تکنولوژیهای تولید فولاد خام در جهان، به جرات میتوان قضاوت کرد. در گذشته و به دلیل ارزان بودن انرژی و دسترسی به ذخایر سرشار گاز طبیعی، تکنولوژی بسیار سخاوتمندانهای به عنوان روش اصلی تولید فولاد در ایران انتخاب شده و بنابراین عمده تولید فولاد خام ایران از آن زمان تاکنون بر همین اساس بنا نهاده شده است. تصویر کلی این ادعا به این صورت است که برای به دست آوردن یک تن فولاد خام، علاوه بر مصرف حدود ۲٫۵ تن سنگآهن، در حدود ۴۰۰ تا ۵۰۰ متر مکعب گاز و حدود یک هزار کیلووات ساعت برق مصرف میشود و متاسفانه این اعداد زمانی رنگ واقعیت به خود میگیرند و در دید ناظر بیرونی قابل توجه جلوه میکنند که باید در حدود ۲۰ درصد از مذابی که با این حجم از انرژی تولید شده است، به عنوان سرباره کوره اصلی دور ریخته شود و عملا در شرایط فعلی کشور که با بحران انرژی روبهرو هستیم، بخش عمدهای از این انرژی گرانقیمت برای تولید ضایعات جانبی فرایندهای تولید فولاد خام درکشور در حال از دست رفتن است.
علاوهبراین در تابستان، مشکلات برق و در زمستان، معضلات گاز صنایع سبب از بین رفتن حداقل ۲۰ درصد از ظرفیت تولید کشور شده است. از سوی دیگر، افزایشات مداوم هزینههای انرژی و صدور قبوض «علیالحساب» طی سالیان اخیر و سایه «عطف به ما سبق» شدن آنها و در واقع ترس از ایجاد هزینههای جدید تولید برای محصولی که مدتها قبل تولید و بعضا فروخته شده، سبب افزایش این نااطمینانی شده است. به صورت کلی، میزان مصرف انرژی در بخشهای مختلف زنجیره تولید فولاد در نمودار ذیل آورده شده است.
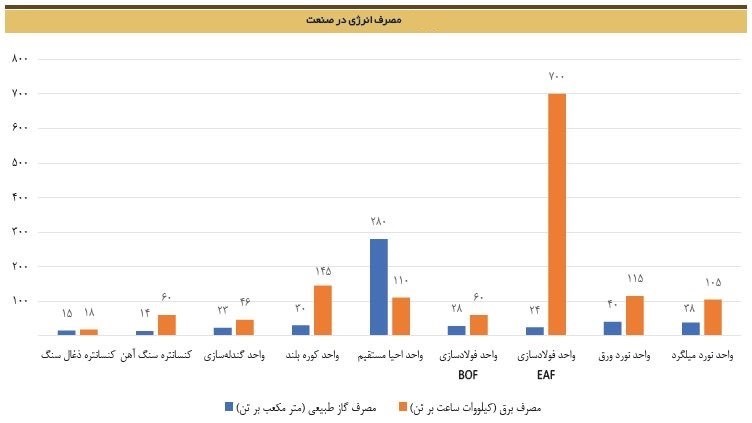
از سوی دیگر و به روایت آمارهایی که توسط انجمن تولیدکنندگان فولاد ایران ارائه شده، در سال گذشته صرفا ۲۴ میلیون تن از ۳۲ میلیون تن فولاد میانی تولید شده در کشور مصرف شده است. به عبارتی، حداقل ۲۵ درصد از ظرفیت تولید فولاد کشور به صورت مازاد بر نیاز تولید میشود که متاسفانه دستورالعملهای متعدد و بعضا «دفعتا لازمالاجرا» به خصوص در زمینه صادرات و برگشت ارز حاصل از صادرات، سبب افت ۵۰ درصدی صادرات اسلب و ۲۶ درصدی فولاد میانی در سه ماهه ابتدایی سال جاری شده است؛ آن هم برای صنعتی که ۲۵ درصد تولید مازاد بر نیاز دارد.
آن روی سکه این حجم از کاهش میزان صادرات، افزایش عرضه در بازار داخل است که متاسفانه میتواند به عنوان یکی از دلایل شرایط رکودی فعلی بازار فولاد کشور باشد. دستورالعمل اخیر برگشت ارز حاصل از صادرات (چه محصولی که به صورت ارزی فروخته شده و چه محصولی که در رینگ صادراتی بورس کالا فروخته شده و قرار است خریدار آن را اظهار کند و متعهد بازگرداندن ارز حاصل از صادرات آن باشد)، در کنار نرخهای ارز در سامانه نیما را میتوان اصلیترین دلایل افت شدید صادرات و رکود در بازار داخل دانست.
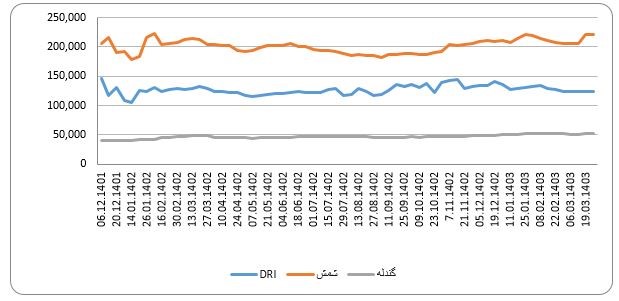
نمودار فوق روند قیمت گندله، شمش فولادی و آهن اسفنجی را از سال ۱۴۰۱ نشان میدهد. همانگونه که گفته شد، شرایط رکودی بازار فولاد را میتوان در دامنه تغییرات قیمت شمش و آهن اسفنجی به وضوح مشاهده کرد. عامل دیگری که به عنوان چالش بعدی فولادسازان در شرایط کنونی میتوان نام برد، عدم توازن در زنجیره فولاد است که اثر آن را در نمودار بالا به وضوح میتوان دید؛ به نحوی که علیرغم افزایش ۳۰ درصدی قیمت گندله از سال ۱۴۰۱، متاسفانه روند قیمتی شمش بیلت در دامنه ۱۸ هزار تا ۲۲ هزار در طول این مدت در نوسان بوده است.
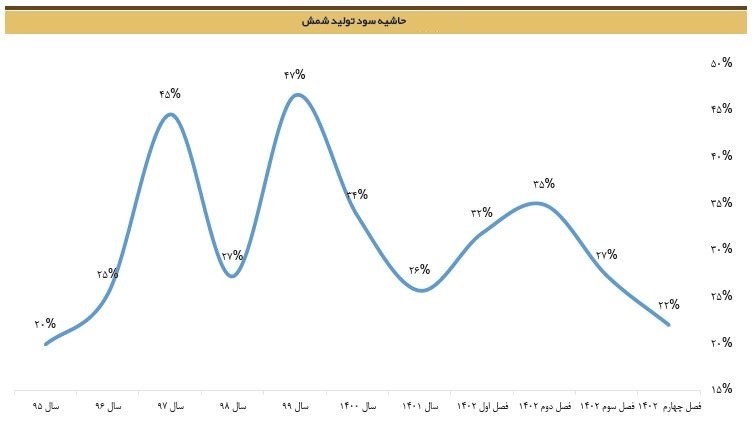
در نمودار فوق، روند حاشیه سود صنعت فولاد در بخش تولید شمش آورده شده است. همانگونه که مشاهده میشود، اثر جمیع عواملی که در بالا ذکر شده، به وضوح در روند حاشیه سود این صنعت منعکس شده است و به عبارتی میتوان به صرف استناد به این نمودار دغدغهای که در ابتدا عنوان شد را به تصویر کشید. از نگاه متخصصان امر، در شرایط کنونی ناجی این صنعت، حمایت دولت و نهادهای بالادستی در بخشهای مختلف خصوصا در تسهیل فضای کسبوکار است. متاسفانه دستورالعملهای متعدد و تشدید مشکلات تامین سرمایه در گردش مهمترین موضوعی است که باید در اسرع وقت ساماندهی شود.
اختصاص اعتبارات بلندمدت جهت بهینهسازی و بهروزرسانی ماشینآلات به منظور افزایش راندمان خط تولید و کاهش ضایعات، در کنار تسهیل شرایط صادرات (از روشهای برگشت ارز تا رفع عوارض و مالیات محصولات صادراتی) به منظور افزایش ظرفیتهای ارزآوری کشور از جمله عوامل دیگری است که باید دولت و نهادهای بالادستی برای احیای این صنعت به آن اهتمام ورزند.
با توجه به هزینههای گزاف مصرف شده در تولید و استحصال ضایعات سرباره، خرسک، ته تاندیش و سایر ضایعات غیرقابل اجتناب خط تولید، شرکت آهن و فولاد ارفع در زمینه بهینهسازی و افزایش راندمان خط تولید و افزایش ظرفیت واحد احیا و فولادسازی اقدامات متعددی انجام داده که منجر به افزایش ۲۵ درصدی ظرفیت تولید واحد فولادسازی و ۵۰ درصدی ظرفبت واحد احیا شده است و همین موضوع، سبب ثبت رکوردهای پی در پی در واحدهای فولادسازی و احیا شده است. از سوی دیگر، این شرکت به منظور بازیافت ضایعات خط تولید اقدام به خرید و نصب ماشینآلات خردایش و بازیافت ضایعات فلزی خط تولید کرده است.
همانگونه که عنوان شد، متاسفانه بحران انرژی و قطعی برق در تابستان و گاز در زمستان، سبب از دست رفتن بخشی از ظرفیت تولید شرکت شده است. بر همین اساس شرکت آهن و فولاد ارفع اقدام به اجرای طرح ذخیرهسازی گاز طبیعی مایع جهت مقابله با افت فشار گاز در زمستان و احداث نیروگاه خودتامین جهت تامین برق در تابستان کرده و امید است با بهرهگیری از تلاش شبانهروزی نیروهای متخصص شرکت و اقدامات اتخاذ شده، بخشی از حاشیه سود از دست رفته بازیابی شود.
انتهای پیام//
مصطفی چمران، معاون فروش شرکت آهن و فولاد ارفع طی یادداشتی نوشت:
صنعت فولاد در گیرودار چالشهای متعدد
در یک نگاه کلی و از نقطه نظر روشهای مرسوم تولید فولاد در ایران و در مقایسه با تکنولوژیهای تولید فولاد خام در جهان، به جرات میتوان قضاوت کرد. در گذشته و به دلیل ارزان بودن انرژی و دسترسی به ذخایر سرشار گاز طبیعی، تکنولوژی بسیار سخاوتمندانهای به عنوان روش اصلی تولید فولاد در ایران انتخاب شده و بنابراین عمده تولید فولاد خام ایران از آن زمان تاکنون بر همین اساس بنا نهاده شده است. تصویر کلی این ادعا به این صورت است که برای به دست آوردن یک تن فولاد خام، علاوه بر مصرف حدود ۲٫۵ تن سنگآهن، در حدود ۴۰۰ تا ۵۰۰ متر مکعب گاز و حدود یک هزار کیلووات ساعت برق مصرف میشود و متاسفانه این اعداد زمانی رنگ واقعیت به خود میگیرند و در دید ناظر بیرونی قابل توجه جلوه میکنند که باید در حدود ۲۰ درصد از مذابی که با این حجم از انرژی تولید شده است، به عنوان سرباره کوره اصلی دور ریخته شود و عملا در شرایط فعلی کشور که با بحران انرژی روبهرو هستیم، بخش عمدهای از این انرژی گرانقیمت برای تولید ضایعات جانبی فرایندهای تولید فولاد خام درکشور در حال از دست رفتن است.
علاوهبراین در تابستان، مشکلات برق و در زمستان، معضلات گاز صنایع سبب از بین رفتن حداقل ۲۰ درصد از ظرفیت تولید کشور شده است. از سوی دیگر، افزایشات مداوم هزینههای انرژی و صدور قبوض «علیالحساب» طی سالیان اخیر و سایه «عطف به ما سبق» شدن آنها و در واقع ترس از ایجاد هزینههای جدید تولید برای محصولی که مدتها قبل تولید و بعضا فروخته شده، سبب افزایش این نااطمینانی شده است. به صورت کلی، میزان مصرف انرژی در بخشهای مختلف زنجیره تولید فولاد در نمودار ذیل آورده شده است.
از سوی دیگر و به روایت آمارهایی که توسط انجمن تولیدکنندگان فولاد ایران ارائه شده، در سال گذشته صرفا ۲۴ میلیون تن از ۳۲ میلیون تن فولاد میانی تولید شده در کشور مصرف شده است. به عبارتی، حداقل ۲۵ درصد از ظرفیت تولید فولاد کشور به صورت مازاد بر نیاز تولید میشود که متاسفانه دستورالعملهای متعدد و بعضا «دفعتا لازمالاجرا» به خصوص در زمینه صادرات و برگشت ارز حاصل از صادرات، سبب افت ۵۰ درصدی صادرات اسلب و ۲۶ درصدی فولاد میانی در سه ماهه ابتدایی سال جاری شده است؛ آن هم برای صنعتی که ۲۵ درصد تولید مازاد بر نیاز دارد.
آن روی سکه این حجم از کاهش میزان صادرات، افزایش عرضه در بازار داخل است که متاسفانه میتواند به عنوان یکی از دلایل شرایط رکودی فعلی بازار فولاد کشور باشد. دستورالعمل اخیر برگشت ارز حاصل از صادرات (چه محصولی که به صورت ارزی فروخته شده و چه محصولی که در رینگ صادراتی بورس کالا فروخته شده و قرار است خریدار آن را اظهار کند و متعهد بازگرداندن ارز حاصل از صادرات آن باشد)، در کنار نرخهای ارز در سامانه نیما را میتوان اصلیترین دلایل افت شدید صادرات و رکود در بازار داخل دانست.
نمودار فوق روند قیمت گندله، شمش فولادی و آهن اسفنجی را از سال ۱۴۰۱ نشان میدهد. همانگونه که گفته شد، شرایط رکودی بازار فولاد را میتوان در دامنه تغییرات قیمت شمش و آهن اسفنجی به وضوح مشاهده کرد. عامل دیگری که به عنوان چالش بعدی فولادسازان در شرایط کنونی میتوان نام برد، عدم توازن در زنجیره فولاد است که اثر آن را در نمودار بالا به وضوح میتوان دید؛ به نحوی که علیرغم افزایش ۳۰ درصدی قیمت گندله از سال ۱۴۰۱، متاسفانه روند قیمتی شمش بیلت در دامنه ۱۸ هزار تا ۲۲ هزار در طول این مدت در نوسان بوده است.
در نمودار فوق، روند حاشیه سود صنعت فولاد در بخش تولید شمش آورده شده است. همانگونه که مشاهده میشود، اثر جمیع عواملی که در بالا ذکر شده، به وضوح در روند حاشیه سود این صنعت منعکس شده است و به عبارتی میتوان به صرف استناد به این نمودار دغدغهای که در ابتدا عنوان شد را به تصویر کشید. از نگاه متخصصان امر، در شرایط کنونی ناجی این صنعت، حمایت دولت و نهادهای بالادستی در بخشهای مختلف خصوصا در تسهیل فضای کسبوکار است. متاسفانه دستورالعملهای متعدد و تشدید مشکلات تامین سرمایه در گردش مهمترین موضوعی است که باید در اسرع وقت ساماندهی شود.
اختصاص اعتبارات بلندمدت جهت بهینهسازی و بهروزرسانی ماشینآلات به منظور افزایش راندمان خط تولید و کاهش ضایعات، در کنار تسهیل شرایط صادرات (از روشهای برگشت ارز تا رفع عوارض و مالیات محصولات صادراتی) به منظور افزایش ظرفیتهای ارزآوری کشور از جمله عوامل دیگری است که باید دولت و نهادهای بالادستی برای احیای این صنعت به آن اهتمام ورزند.
با توجه به هزینههای گزاف مصرف شده در تولید و استحصال ضایعات سرباره، خرسک، ته تاندیش و سایر ضایعات غیرقابل اجتناب خط تولید، شرکت آهن و فولاد ارفع در زمینه بهینهسازی و افزایش راندمان خط تولید و افزایش ظرفیت واحد احیا و فولادسازی اقدامات متعددی انجام داده که منجر به افزایش ۲۵ درصدی ظرفیت تولید واحد فولادسازی و ۵۰ درصدی ظرفبت واحد احیا شده است و همین موضوع، سبب ثبت رکوردهای پی در پی در واحدهای فولادسازی و احیا شده است. از سوی دیگر، این شرکت به منظور بازیافت ضایعات خط تولید اقدام به خرید و نصب ماشینآلات خردایش و بازیافت ضایعات فلزی خط تولید کرده است.
همانگونه که عنوان شد، متاسفانه بحران انرژی و قطعی برق در تابستان و گاز در زمستان، سبب از دست رفتن بخشی از ظرفیت تولید شرکت شده است. بر همین اساس شرکت آهن و فولاد ارفع اقدام به اجرای طرح ذخیرهسازی گاز طبیعی مایع جهت مقابله با افت فشار گاز در زمستان و احداث نیروگاه خودتامین جهت تامین برق در تابستان کرده و امید است با بهرهگیری از تلاش شبانهروزی نیروهای متخصص شرکت و اقدامات اتخاذ شده، بخشی از حاشیه سود از دست رفته بازیابی شود.
انتهای پیام//
با توجه به برآوردهای صورت گرفته،
طی سالهای آتی به وقوع خواهد پیوست؛
در پی شهادت جمعی از مردم در تجاوز نظامی رژیم صهیونیستی
هدفگذاری شد
مدیرعامل گروه فولاد مبارکه عنوان کرد:
در مجمع عمومی عادی سالیانه مطرح شد؛
رضا طالبی، مدیرعامل شرکت صنعتی و معدنی اپال پارسیان سنگان در گفتوگو با «فلزاتآنلاین»:
علی امرایی، مدیرعامل شرکت صنایع معدنی فولاد سنگان در گفتوگو با «فلزاتآنلاین»:
علیرضا شریفی، مدیر تحقیق و توسعه شرکت مهندسین مشاور پیشگامان فولاد جنوب در گفتوگو با «فلزاتآنلاین»:
امین صفری، مدیرعامل شرکت آهن و فولاد ارفع در گفتوگو با «فلزاتآنلاین»:
رضا طالبی، مدیرعامل شرکت صنعتی و معدنی اپال پارسیان سنگان در گفتوگو با «فلزاتآنلاین»:
علیرضا مخبر دزفولی، قائم مقام مدیرعامل شرکت فولاد خوزستان در امور ستادی و مسئولیتهای اجتماعی در گفتوگو با «فلزاتآنلاین»:
مدیرعامل شرکت صنعت فولاد شادگان طی یادداشتی در «فلزاتآنلاین» نوشت:
بهرام سبحانی، رئیس هیئت مدیره انجمن تولیدکنندگان فولاد ایران طی یادداشتی در «فلزاتآنلاین» نوشت:
ابراهيم جانقربانيان، عضو هيئت مديره و معاون بازرگانی شرکت صبا فولاد خليج فارس طی یادداشتی در «فلزاتآنلاین» نوشت:
حسين کاظمیمهر، نايب رئيس هيئت مديره شرکت مجتمع فولاد و نورد آسين ابهر طی یادداشتی در «فلزاتآنلاین» نوشت:
سید رضا شهرستانی، مدیرعامل شرکت لوله و اتصالات چدنی (کلاچ) طی یادداشتی در «فلزاتآنلاین» نوشت:
صادق قاسمی فلاورجانی، مديرعامل شرکت فنی مهندسی آرين مدرن جهانآرا طی یادداشتی نوشت:
در دو ماهه نخست 1404 حاصل شد؛
تعبیر وارونه یک رویا؛
در برهه زمانی 24-2015 صورت پذیرفت؛
«فلزاتآنلاین» گزارش میکند:
همگام با اجرای طرحهای توسعهای،
در سال 2025 محقق خواهد شد؛
در مجمع عمومی عادی سالیانه «ارفع» مطرح شد؛
در نشست خبری مدیرعامل شرکت فولاد خوزستان مطرح شد؛
با هدف رشد تولید انجام خواهد شد؛
«کگهر» در مسیر توسعه و رشد سودآوری؛
با تایید سهامداران در مجمع فوقالعاده،
«فلزاتآنلاین» گزارش میکند:
خط تولید فولادسازی شرکت صنعت فولاد شادگان با موفقیت وارد مدار شد
انجام موفق و بدون مغایرت انبارگردانی سالانه سیمیدکو
نگاه ویژه مسئولان به شرکت فولاد اکسین خوزستان
تلاش مشترک برای بهبود تولید در کارگاه چدنریزی «ذوب»
کلنگزنی و افتتاح پروژههای توسعهای فولاد سنگان با حضور وزیر صمت
آیین افتتاح پروژههای منطقه معدنی و صنعتی گلگهر
اینفوگرافیک شرکت فولاد سرمد ابرکوه؛
اینفوگرافیک شرکت معدنی و صنعتی چادرملو؛
اینفوگرافیک شرکت معدنی و صنعتی گهرزمین؛
اینفوگرافیک شرکت فولاد هرمزگان؛
اینفوگرافیک فولاد خراسان؛
اینفوگرافیک شرکت فولاد خوزستان؛
گزارش تصویری از
گزارش تصویری از
گزارش تصویری از
گزارش تصویری از
گزارش تصویری از
گزارش تصویری از
گزارش تصویری از
شاخصهای قیمتی فلزات آنلاین
شمش آلومینیوم
فلزات آنلاین
1404/03/26
224083
ورق برنجی
فلزات آنلاین
1404/03/26
858230
ورق مسی
فلزات آنلاین
1404/03/26
1374431
لوله مسی
فلزات آنلاین
1404/03/26
1331305
بیلت فولادی داخلی
فلزات آنلاین
1404/03/26
29819
آهن اسفنجی
فلزات آنلاین
1404/03/26
16025
ورق اسیدشویی
فلزات آنلاین
1404/03/26
45904
لوله بدون درز
فلزات آنلاین
1404/03/26
65099
لوله اسپیرال
فلزات آنلاین
1404/03/26
47680
لوله صنعتی
فلزات آنلاین
1404/03/26
42960
تیرآهن
فلزات آنلاین
1404/03/26
41121
ناودانی
فلزات آنلاین
1404/03/26
38054
نبشی
فلزات آنلاین
1404/03/26
37017
پروفیل صنعتی
فلزات آنلاین
1404/03/26
43017
ورق سیاه
فلزات آنلاین
1404/03/26
38549
ورق رنگی
فلزات آنلاین
1404/03/26
59174
میلگرد آجدار
فلزات آنلاین
1404/03/26
35071
ورق روغنی
فلزات آنلاین
1404/03/26
43385
ورق گالوانیزه
فلزات آنلاین
1404/03/26
59056
طلای ۱۸ عیار
فلزات آنلاین
1404/03/26
6774100